From hand-cut joinery to hydraulic presses, the truss tells a story of steady progress
Trusses are the quiet giants of structural engineering, turning simple triangles into some of the strongest, most efficient shapes in construction. Triangles have carried roofs since the days of ancient temples, yet the craft of turning raw lumber into reliable trusses has revolutionized the building industry. The geometry stayed the same, but the tools, techniques, and speed of production evolved dramatically once a small steel plate entered the scene.
Early Ingenuity and the Use of Mass Timber
Long before machinery hummed on a factory floor, Greek and Roman builders used wooden trusses to bridge wide spaces where stone arches could not reach. Every joint was carved by hand, secured with pegs or wooden pins, and checked by an experienced eye.
Gothic and Renaissance carpenters pushed the craft further. Mortise-and-tenon joints, curved braces, and hand-hewn beams produced soaring cathedral roofs and castle halls. The results were beautiful, but progress depended on slow, meticulous labor and the rare skill of the local carpenter.
The Industrial Age Sets the Stage
Steel let engineers stretch bridges across rivers, yet in houses and small commercial buildings wood remained king. By the early twentieth century most timber trusses were still cut and assembled one at a time. Nails, bolts, and wooden pegs held members together, but none of those fasteners made mass production easy.
That changed in the middle of the century.
Milestones that Reshaped Wood Truss Manufacturing
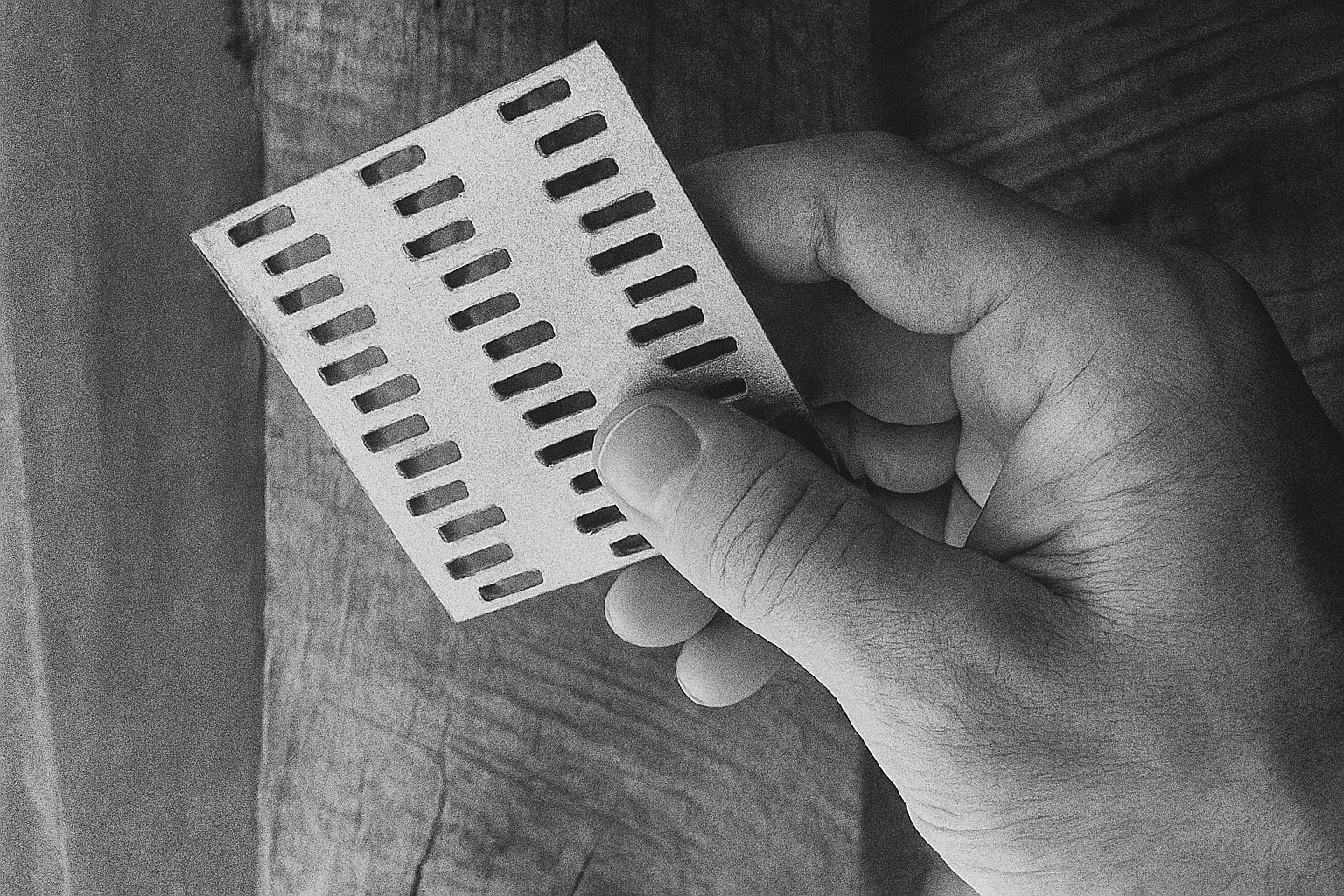
How Factories Transformed Residential Construction
When connector plates began to be pressed rather than nailed, truss plants started to resemble small assembly lines. Hydraulic presses set plates in a single motion, automated saws cut every chord and web to precise lengths, and computer-aided design let engineers send digital layouts straight to the shop floor. By the early 1980s, software vendors, machinery suppliers, lumber brokers, and component plants were working from the same playbook, so the cost of a roof truss fell while quality rose.
What that meant on site. Builders could now frame roofs in hours, not days, and they were no longer limited to simple rectangles. The new equipment made it easy to create long, clear spans for open-concept living rooms, vaulted ceilings, and complex hips and valleys that once belonged only to custom homes. Wider garages, bonus rooms over the garage, and sweeping porches all became affordable options for mainstream construction.
Proprietary Plate Silos
File formats differences and plate exclusivity started to create problems. Engineering seals, load tables, and warranty coverage were tied to one brand of connector plate. Switching suppliers meant redrawing every layout with new tooth patterns, recalculating loads, and paying for fresh seals. Keeping two brands on the floor required extra licensing and support fees. The hassle pushed most plants to commit to a single plate supplier and stick with it, even if another vendor later offered better pricing or new features.
The tools that once accelerated production eventually slowed collaboration. Designs, data, and innovation became trapped inside closed platforms.
The Next Leap Forward
At Paragon we see the future of truss design in openness and intelligence. Open APIs, cloud collaboration, and smart design tools can unlock the rich data already living inside every truss file. When information flows freely, shops gain flexibility, engineers experiment faster, and builders get to site with fewer surprises.
The truss has always proven how simple shapes can carry heavy loads. It is time the software that supports it did the same.
Curious about a more open workflow?
Create a free Paragon account and explore the next chapter in open truss design technology.